IoT in Oil & Gas Industry
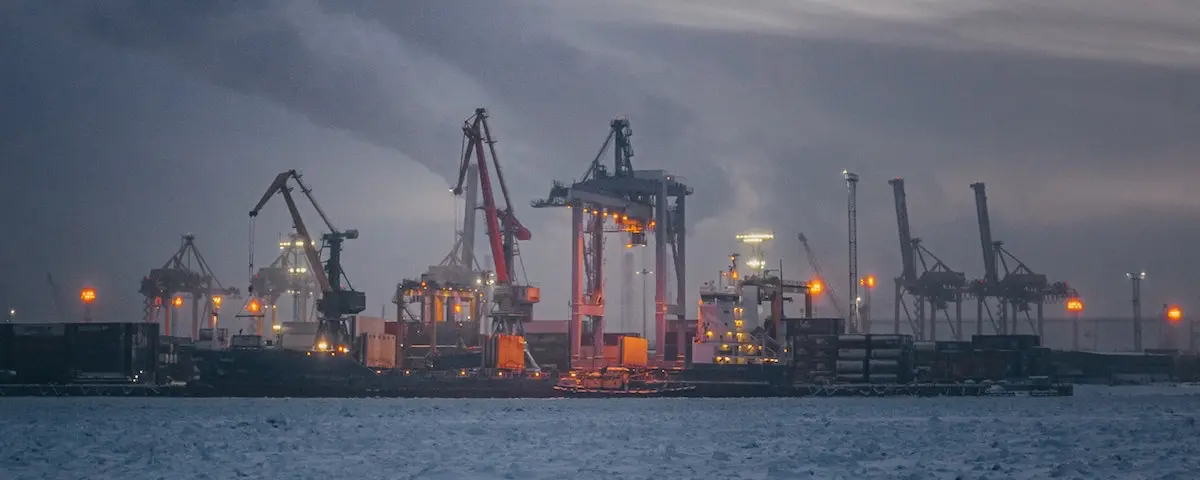
Almost every article on the oil and gas (O&G) industry claims that $100/barrel of oil may not be seen again for a very long time. When you factor in the fact that customers are increasingly looking for a better digital experience when shopping for downstream oil and gas companies (companies that process, sell, and distribute oil-based products), you have a situation in which prices are uncertain and downstream oil and gas companies no longer benefit from competitive prices alone. These worries increase the likelihood that oil and gas businesses will adopt these IoT technologies.
One of the main advantages of oil and gas IoT applications is creating value for the oil and gas industry via an integrated deployment strategy. Because of IoT, organizations can digitize, optimize, and automate formerly disjointed processes, resulting in cost savings, improved efficiency, and enhanced employee security. The following paragraphs will examine how the IoT might benefit the oil and gas sector.
Off-Site Maintenance Companies
Petroleum is seldom found in convenient locations. Because of IoT, oil and gas companies can respond immediately to incidents like spills, emergency shutdowns, and remote field operations, no matter the time of day or night. Extraction sites are often in inaccessible locations, safety and regulatory issues are increasing, and the expense of maintaining equipment is rising. The pace at which a problem may be identified and fixed in the field is considerably delayed without using connected monitoring equipment.
The combination of predictive and preventative maintenance
The overwhelming majority of oil and gas production facilities need routine inspections. This is made possible by remote services, enabling establishments to deal with problems using preventative maintenance. Because this includes the daily monitoring of tank levels, pressure, and flow rates, in addition to several other controls, these devices are not immune to wear and tear and typically need regular maintenance.
Healthy Living and Threat Assessment
Generally speaking, oil and gas facilities are not situated near neighborhood grocery shops. Most are located in ecologically and humanely damaging inhospitable oases of wilderness, where neither human nor animal life can thrive. Reservoirs offshore may be submerged as deep as 3,000 meters, and rigs can be situated relatively far offshore, often near fault lines where dangerous occurrences might occur at any time.
According to the CDC, there were 602 incidents involving oil and gas extraction workers between January 2015 and January 2017, resulting in 481 hospitalizations and 166 amputations.
It's common knowledge that catastrophes may cause severe monetary setbacks. Implementing safety measures made feasible by the internet of things can help oil and gas companies not only ensure the well-being of their employees but also reduce their legal exposure and increase their bottom line.
Keeping a Close Eye on Your Resources
There is a constant demand in the oil and gas industry to improve safety and operational performance and generate considerable financial returns. Because of this, oil and gas IoT applications using wireless sensor networks for asset tracking and equipment monitoring have seen the most significant growth. Companies are devoting more resources to analyzing their investments and internal operations due to the oil price fluctuations to find areas where costs can be cut or processes can be altered without jeopardizing the company while achieving the highest possible asset utilization.
To a large extent, the success or failure of an organization's operations may be attributed to how well its assets are managed. Enterprise asset management and the standardization of production may improve operational productivity by making the output more stable and reliable (EAM).
Asset monitoring enables businesses to digitally adapt their processes and keep tabs on various wells and locations simultaneously. The consolidation of property into a unified whole allows for this. A single pump failure, for instance, may cost a company $300,000, not including the lost productivity from a day's downtime.
IoT sensors provide for more accurate and economical monitoring of vital pipeline machinery. Businesses may use it to research prospective drilling locations, locate the exact spot where a new pump and filter should be put, and learn more about the process overall. Thanks to sensors, oil companies can track much more than just oil and gas deliveries and stock levels.
Businesses benefit greatly from the information these tracking devices provide, allowing for a more precise inventory count. If an oil or gas asset goes stolen, an Internet of Things system might be utilized to track deliveries and pinpoint their whereabouts.
Administrative Control of Information
Due to the prevalence of disruptive technologies and data availability, O&G businesses have been driven to undertake the digital transformation necessary to bring themselves up to speed with newly linked technologies. With millions of connected devices at their disposal, O&G companies will be able to amass a mountain of data. Because of this, they can implement risk-free, efficient, and successful practices that will pave the way for transformation. Integrating data in a way that is relevant to data quality and taking this data and analyzing it in real-time for the goal of generating operational benefits is a significant challenge for oil and gas companies.
Large refineries generate one terabyte of raw data daily, whereas utility companies may analyze 1.1 billion data points daily. Because of this, it may be difficult for organizations to get insights from their data since their equipment may be located in distant locations with limited network connectivity or high bandwidth prices, prohibiting data from being uploaded to the cloud.
Moving all the data from the several locations and formats used by energy companies to a central place where it can be processed and assessed may be challenging. Data virtualization is merging disparate data sources into a single logical database for the convenience of end users. Data virtualization may be helpful for anybody collecting information from a wide range of remote heads since it reduces the need to store that information in a centralized location (sensors, video cameras, third-party influencers, etc.).
Since the system is built to integrate data in real-time, data virtualization removes the need to store all data in one central location physically. "On-demand" integration means that information may be accessed instantly whenever it's needed. Businesses may access and modify information regardless of the data's physical location or storage type.
Offshore oil platforms often utilize a satellite connection to transmit data. Still, it would take more than 12 days to convey just one day's worth of data to a central location, making it too old to be useful.
No one has to be reminded that data serves no use unless it is analyzed and put to good use. The use of edge computing in O&G operations has the potential to increase production efficiency and accuracy and decrease risk. This enables businesses to continuously monitor and act upon critical data as it is being acquired.
Perspectives on IoT Implementation in the Oil and Gas Sectors
Businesses in the oil and gas sector that use IoT technologies will be better able to boost productivity, respond to customer needs in real-time, and open new markets. An integrated framework in which IoT applications and deployments are carefully monitored throughout the ecosystem of upstream, midstream, and downstream businesses is advantageous for the oil and gas sector, which is highly fragmented and encompasses many distinct streams.
Explore more
Need any help in IoT?
Need any help in IoT? An Atreyo expert identify the right solution for your needs.
If ready to talk to an Atreyo expert
Interested in IoT products? go to